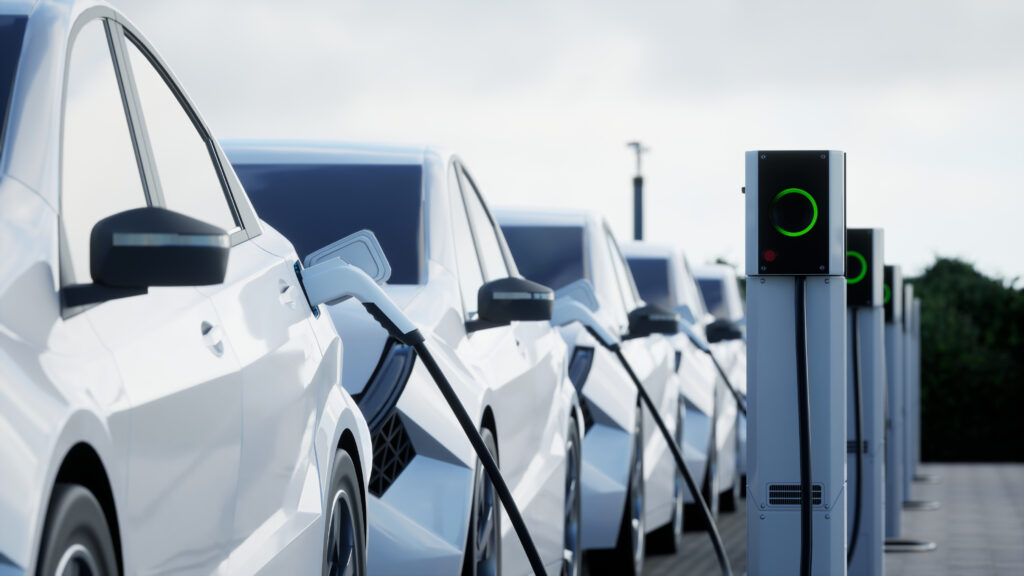
The automotive industry is undergoing a significant transformation, with the shift from internal combustion engine vehicles to electric vehicles (EVs) at the forefront of this change. One critical yet often overlooked component in the design and manufacturing of EVs is automotive fasteners – essential building blocks that ensure the safety, efficiency, and performance of electric vehicles. Here, we delve into the role of automotive fasteners in EVs, highlighting their importance in various aspects of vehicle construction, from battery systems to vehicle electronics.
The Importance of Automotive Fasteners in EVs
Fasteners, including screws, bolts, pins, and clamps, are integral to the assembly and operation of electric vehicles. They hold together the car body, secure the battery systems, and ensure that the vehicle electronics function as they should. Unlike traditional vehicles—where fasteners are primarily used to secure components like the engine and fuel flow systems—EVs require fasteners that are compatible with their unique components, such as electric motors, battery packs, and advanced electronics.
Challenges in Fastening for EVs
The transition to electric vehicles presents several challenges to fastener manufacturers. One primary consideration is the weight of the vehicle. EV manufacturers are constantly seeking ways to reduce the overall weight of their vehicles to increase efficiency and extend the battery range, which has led to the use of lightweight materials like aluminium, titanium, and plastic fasteners in place of traditional metal fasteners. However, these materials must still provide the strength and durability required to withstand the stresses of daily use and ensure the safety of the vehicle.
Fasteners in Battery Systems
The battery system is the heart of the electric vehicle, and securing it is of utmost importance. Automotive fasteners used in battery systems must withstand high levels of vibration, temperature fluctuations, and exposure to corrosive substances. Stainless steel fasteners are often used in these applications due to their corrosion resistance and ability to maintain their integrity in harsh environments.
Additionally, the design of battery systems requires a combination of different types of fasteners. For instance, bolts may be used to secure the battery housing, while clamps and screws are employed to hold individual battery cells in place. In combination, these fasteners ensure the overall stability and safety of the battery system, which is crucial for the vehicle’s performance and the safety of its occupants.
Fasteners in Vehicle Electronics
The role of fasteners in vehicle electronics is another critical aspect of EV design. Electric vehicles rely on complex electronic systems to control everything from the motors to the instrument panel and auxiliary equipment. Fasteners used in these applications provide a secure connection while also protecting the delicate electronic components from vibration and thermal expansion.
Lightweight plastic fasteners are often used in vehicle electronics for their non-conductive properties, which helps prevent electrical shorts and interference. These fasteners are particularly useful in securing the centre console, cockpit components, and the instrument panel, where the integrity of the electronics is paramount.
Fasteners in Electric Motors and Drivetrain
The electric motor is another vital component of an EV, converting electrical energy into mechanical energy to propel the vehicle. The assembly of the motor and its connection to the drivetrain require precision-engineered fasteners that can withstand the high torque and rotational forces generated during operation. Industrial fasteners, such as bolts and clamps, secure the motor to the vehicle’s frame and connect it to the gearbox and clutch systems.
Given the high levels of vibration and stress associated with the operation of electric motors, fasteners used in these applications must be durable and remain tight over time. This is especially important in the gearbox, where the alignment of the components must be maintained for smooth and efficient power transmission.
Security and Safety Considerations
In addition to their function, fasteners in electric vehicles also serve as a security measure. Tamper-resistant fasteners, such as security screws and imperial fasteners, are used in critical areas of the vehicle to prevent unauthorised access. These fasteners are employed in areas such as the battery compartment, vehicle electronics, and auxiliary equipment, where the integrity of the components is vital.
Moreover, the use of specific fasteners as a security measure helps protect against theft and tampering, particularly in the case of valuable components like battery packs and motors. The design and selection of these fasteners must balance the need for security with the requirements for ease of maintenance and repair.
Material Considerations for EV Fasteners
The materials used in the manufacture of automotive fasteners for electric vehicles are another critical consideration. Stainless steel is a common choice due to its strength, durability, and corrosion resistance. However, other materials, such as aluminium and titanium, also reduce weight and improve vehicle efficiency. In some cases, plastic fasteners are preferred for specific applications, particularly in the interior of the vehicle, where they offer a lightweight and non-conductive solution.
The selection of materials for fasteners in EVs must consider factors such as thermal expansion, galvanic corrosion, and the potential for electromagnetic interference. Additionally, the use of dissimilar materials in fastener construction and the components they secure can lead to issues with corrosion and long-term durability, and careful consideration is needed during the design phase.
The Future of Fastening Technology in EVs
As the automotive industry continues to evolve, so too does the technology used in automotive fasteners. Advances in materials science and manufacturing processes are leading to the development of new types of fasteners that offer improved performance, durability, and ease of use. For example, self-piercing rivets and adhesive bonding techniques are being explored as alternatives to traditional mechanical fasteners in some applications, offering potential benefits in terms of weight reduction and structural integrity.
Additionally, the rise of 3D printing and additive manufacturing is opening up new possibilities for the customisation and rapid production of fasteners tailored to specific EV designs. This could lead to greater flexibility in the design and assembly of electric vehicles, allowing manufacturers to optimise the use of fasteners for each application and improve overall vehicle performance.
In conclusion, automotive fasteners play a critical role in the design, assembly, and operation of electric vehicles. From securing battery systems to ensuring the integrity of vehicle electronics and motors, the selection and use of fasteners are essential to the safety and performance of EVs. As the automotive industry continues to innovate and push the boundaries of what is possible with electric vehicles, the role of fasteners will remain a key consideration in the pursuit of safer, more efficient, and more sustainable transportation solutions.
For manufacturers and engineers in the EV sector, understanding the importance of fasteners and their impact on vehicle performance is crucial. By choosing the right fasteners and materials, and staying abreast of advances in fastening technology, they can ensure that their electric vehicles meet the highest standards of safety and durability.
At JP Aero, we specialise in supplying a diverse selection of quality automotive fasteners for various applications. Whether you need standard, metric, or custom-designed options, we’re the leading experts in the UK.
With years of experience, we’ve amassed extensive expertise in fasteners for industries such as commercial aviation, heavy industry, oil & gas exploration, defence, and now the burgeoning space industry.
If you’re looking to procure innovative fasteners for aerospace, aviation, or any other industry requiring robust fastener applications, don’t hesitate to reach out to our dedicated team today. We’re here to assist you with any fastener-related needs you may have.