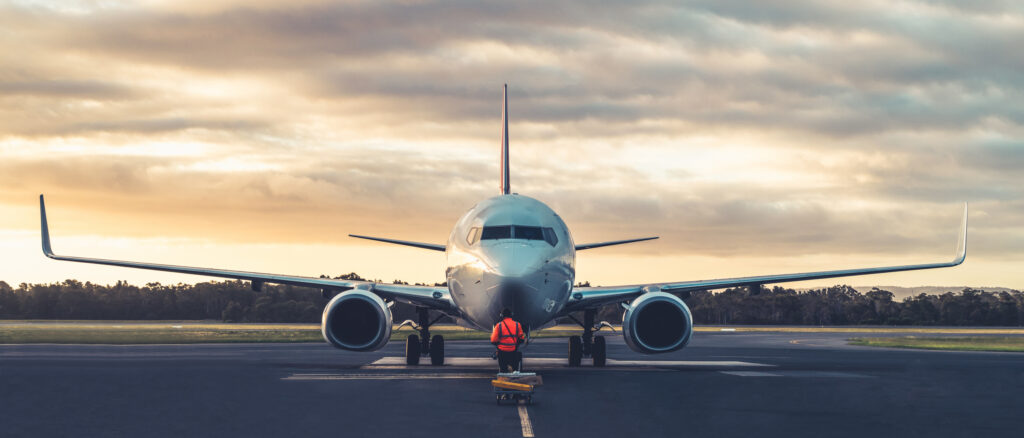
In the aerospace industry, where safety, durability and precision are paramount, corrosion-resistant fasteners ensure critical component longevity, with the choice of fasteners directly impacting performance and safety. Here, we take a close look at the significance of corrosion-resistant fasteners in aerospace applications, the materials and technologies behind their effectiveness, and how they address the unique challenges of corrosive environments.
Understanding Corrosion and Its Impact on Aerospace Fasteners
Corrosion is the gradual degradation of materials—particularly metals—due to chemical reactions with the environment. Aerospace applications expose fasteners to extreme conditions, including salt water, varying temperatures and corrosive elements such as humidity and pollutants. Left unchecked, corrosion compromises the structural integrity of fasteners, leading to failures that can jeopardise an aircraft’s safety.
For instance, galvanic corrosion—where dissimilar metals interact in the presence of an electrolyte—poses a significant challenge. This type of corrosion is particularly common in fasteners used in airframes, where materials like aluminum and stainless steel fasteners come into contact.
Materials for Corrosion-Resistant Fasteners
Selecting the right material with excellent corrosion resistance is the first step in preventing failures. Manufacturers use a variety of metals, alloys and even polymers to meet the demands of aerospace projects.
1. Titanium: Strength and Corrosion Resistance
Titanium fasteners are a staple in aerospace engineering due to their strength and resistance to most types of corrosion. Titanium is also lightweight (and durable), and so ideal for applications in high-stress environments such as jet engines and spacecraft.
2. Stainless Steel: A Versatile Option
Stainless steel fasteners, such as steel bolts and washers, combine high durability with excellent resistance to rust. The addition of chromium and nickel enhances their ability to withstand exposure to corrosive environments like marine or high-humidity regions.
3. Inconel: High Corrosion Resistance in Extreme Conditions
Inconel, a nickel-based alloy, is prized for its ability to resist oxidation (high corrosion) in extreme heat. This makes it a popular choice for aerospace fasteners used in jet engines and exhaust systems.
4. Resistant Polymers and Coatings
While metals dominate, resistant polymer fasteners are gaining traction for certain applications. Their non-metallic nature prevents galvanic corrosion, and they offer a lightweight alternative for securing non-load-bearing components. Additionally, applying a protective coating like Teflon or anodisation to metallic fasteners improves resistance to corrosion.
How Resistant Fasteners Combat Corrosion in Aerospace
The aerospace industry demands solutions that go beyond standard fasteners. Here are ways in which resistant screws and bolts excel in addressing corrosion challenges:
- Protective Barriers: Fasteners with specialised coatings create a protective barrier, shielding the underlying material from corrosive agents.
- Material Selection: The use of the right materials, such as alloys with excellent corrosion resistance, ensures long-lasting performance.
- Design Optimisation: Fasteners are often designed to minimise exposure to corrosive environments, such as embedding them in protective housings.
A good example is the use of stainless steel fasteners in fuselage assemblies, where they must endure temperature fluctuations and potential contact with water or hydraulic fluids.
Specific Applications of Corrosion-Resistant Fasteners in Aerospace
1. Aircraft Structures
Fasteners in aircraft wings and fuselage panels must endure the stresses of flight while resisting corrosion. Using stainless steel or Inconel screws ensures safety in these critical areas.
2. Jet Engines
Jet engines generate extreme heat and are exposed to corrosive elements like exhaust gases. Titanium and Inconel fasteners are ideal for these demanding conditions.
3. Spacecraft Components
Spacecraft experience corrosive environments in orbit due to atomic oxygen and UV radiation. Resistant polymers or fasteners with advanced coatings provide the necessary durability for space missions.
4. Landing Gear Systems
Landing gear systems operate under high mechanical loads and are frequently exposed to salt water and deicing chemicals. Fasteners with resistant properties, such as coated steel bolts, are crucial here.
Advancements in Corrosion-Resistant Fastener Technology
The aerospace industry continuously innovates to address the evolving challenges of corrosion. Modern advancements include:
- Hybrid Materials: Combining metals with polymers for a balance of strength and resistance.
- Smart Coatings: Developing coatings that repair themselves when damaged, prolonging fastener lifespan.
- Advanced Alloys: New alloys like super-austenitic stainless steels offer unparalleled resistance to rust and corrosive elements.
These innovations ensure that fasteners meet the rigorous demands of aerospace applications while reducing the need for frequent replacements.
Choosing the Right Fastener for Aerospace Applications
Selecting the right screw or bolt for an aerospace project requires careful consideration of factors like strength and corrosion resistance, weight and compatibility with other materials.
Key considerations include:
- Environmental Exposure: Will the fastener encounter salt water, humidity or extreme temperatures?
- Load Requirements: Does the application require high tensile strength?
- Material Compatibility: Avoiding galvanic corrosion by selecting compatible materials.
Consulting with suppliers of high quality fasteners like JP Aero ensures the correct fastener selection for specific aerospace applications.
Why Corrosion-Resistant Fasteners Are Essential
Corrosion-resistant fasteners not only enhance the safety and reliability of aerospace structures but also reduce maintenance costs and downtime. By preventing corrosion, these fasteners extend the lifespan of critical components, supporting the industry’s goals of efficiency and sustainability.
For example, fasteners with a protective coating have been shown to reduce maintenance frequency in marine-based aircraft, translating to significant cost savings for operators.
Choosing the right fasteners for your aerospace projects is vital for safety, performance and long-term cost savings. At JP Aero, we specialise in high-quality, corrosion-resistant fasteners tailored to the demanding requirements of the aerospace industry. From titanium and Inconel to advanced resistant polymers, our range of products ensures reliability in the most challenging conditions.
Over the years we have built up a broad depth of knowledge around all types of fasteners in commercial aviation, heavy industry, oil & gas exploration, defence and now the space industry.
Contact us today to learn more about our extensive inventory or to discuss custom solutions for your specific needs. We’re here to help you secure the future of aerospace innovation.