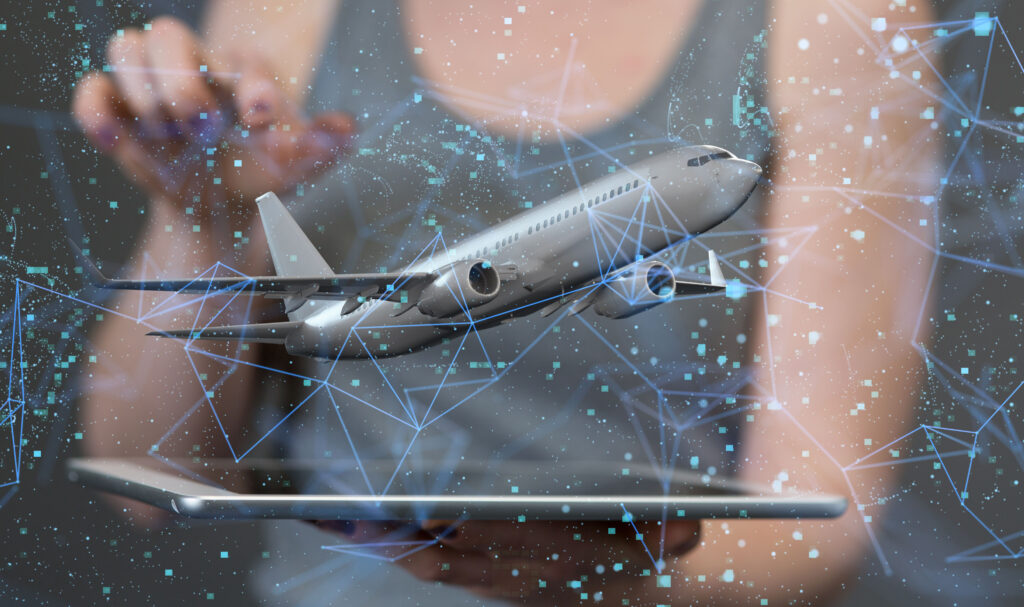
The aerospace manufacturing industry is experiencing a revolutionary shift. Digital technologies are transforming production processes and reshaping supply chains across the globe. From big-hitters like Airbus and Boeing to military-focused companies such as Lockheed Martin and Raytheon Technologies, aerospace companies are embracing innovation to stay competitive. For businesses involved in aerospace fasteners, components and systems, it’s a transformation that presents challenges – but also growth opportunities.
Here, we’ll explore the digital transformation of aerospace manufacturing, looking closely at the UK aerospace sector and the role of the main players involved.
The State of UK Aerospace Manufacturing
The UK plays an important role in the global aerospace industry. The country is home to world-leading companies that design and manufacture a wide range of aerospace products, from aircraft and military vehicles to components such as fasteners and systems. UK aerospace accounts for billions in exports and provides employment to thousands. The sector’s companies must innovate to remain competitive and meet the escalating demand for efficiency and sustainability.
As digital technologies take centre stage, the country’s aerospace supply chain must adapt to new demands like precision engineering, real-time data analysis and smart manufacturing processes. Fastener manufacturers, for instance, incorporate sensors, AI-driven monitoring and digital thread technologies to enhance product quality and streamline production.
These innovations in materials, processes and software, allow manufacturers to achieve higher levels of accuracy and efficiency.
The Impact of Digitalization on the Aerospace Supply Chain
Digital transformation is reshaping the aerospace supply chain. In the past, aerospace manufacturing involved many manual processes, with long lead times and limited ability to optimise production. Today, digital technologies such as the Internet of Things (IoT), artificial intelligence (AI) and advanced data analytics drive the evolution of the supply chain.
Suppliers of aerospace components are now expected to provide real-time data on production, inventory and performance. This connectivity between manufacturers and suppliers creates a more agile supply chain, where issues can be identified and addressed quickly.
As more companies adopt digital tools, the ability to manage and optimise processes becomes a competitive advantage. Companies that can successfully integrate digital systems into their operations will find themselves better equipped to handle the growing complexity of aerospace production and respond to changing market demands.
Airbus and Boeing: Leading the Charge in Aerospace Digitalization
As two of the largest aerospace companies in the world, Airbus and Boeing have been at the forefront of adopting digital technologies. Both companies are heavily investing in advanced manufacturing techniques, such as automation, 3D printing and digital twins, to enhance efficiency. Boeing, for example, uses a digital twin—a virtual model that simulates the aircraft’s characteristics—of each aircraft in its 787 Dreamliner program. The digital twin allows Boeing to monitor the performance of the aircraft in real-time throughout its lifecycle.
Airbus and Digital Manufacturing
Airbus has long been a leader in aerospace innovation, particularly in the adoption of digital technologies, and is focused on transforming its entire manufacturing process – from design to final assembly. As with the example of Boeing above, Airbus makes use of digital twins to optimise its manufacturing processes. The technology enables engineers to simulate different scenarios and make real-time adjustments before physical production begins.
In addition, Airbus embraces 3D printing, also known as additive manufacturing, to produce lightweight components and systems that reduce fuel consumption and increase aircraft efficiency. Aerospace fasteners, like bolts and screws, play a crucial role in these 3D-printed structures, with each tiny fastener meeting stringent safety and performance standards.
Boeing’s Approach to Smart Manufacturing
Boeing, too, is deeply invested in digitalization, particularly through its smart manufacturing initiatives. The company has implemented advanced robotics and automated systems across its production lines. These technologies improve precision, reduce production time and lower costs. Boeing’s use of augmented reality (AR) allows workers to overlay digital instructions on physical parts during assembly. The technology guarantees high levels of accuracy in the construction of complex systems like wings, fuselages and aircraft components.
The implementation of digital technologies at Boeing has revolutionised its approach to the production of military aircraft and spacecraft as well. The company is working closely with organisations like NASA to develop spacecraft and other aerospace products that push the boundaries of human exploration. These partnerships demonstrate the importance of digital innovation not only for commercial aviation but also for the defence and space sectors.
Fasteners: The Hidden Heroes of Aerospace Innovation
While much of the attention in the global aerospace industry is focused on aircraft design and major systems, it’s often the smaller components, such as fasteners, that hold everything together—literally. Fasteners, including bolts, rivets and screws, provide structural integrity to the aircraft, ensuring that its components remain securely joined under extreme conditions.
Fastener manufacturers in the aerospace sector are under constant pressure to innovate. As aerospace companies demand lighter, stronger and more durable materials, fastener suppliers must develop products that meet these requirements without sacrificing safety or performance. As such, these manufacturers use materials like titanium alloys and carbon composites to reduce weight and improve efficiency.
Precision machining and automation aid fastener manufacturers in producing components with tighter tolerances and greater consistency. This is especially important as modern aircraft designs continue to push the limits of what is possible in terms of speed, altitude and fuel efficiency.
Innovation in Aerospace Products: A Collaborative Effort
Innovation in aerospace manufacturing is rarely a solitary effort. Companies across the industry, from fastener manufacturers to major OEMs like Lockheed Martin, Raytheon Technologies and BAE Systems, are collaborating to develop new products and technologies. The production of aircraft and spacecraft requires a high level of integration, with multiple suppliers working together to create the systems and components that make up the final product.
Challenges and Opportunities in the Aerospace Fastener Industry
The aerospace sector is currently facing a number of challenges, from supply chain disruptions to increased competition. However, significant opportunities exist to capitalise on the ongoing digital transformation.
One of the main challenges is maintaining quality and safety standards while reducing production costs. Aerospace fastener manufacturers, for instance, must ensure that their products meet rigorous certification requirements, which can be costly and time-consuming. At the same time, they need to keep pace with the rapid advancements in technology and materials.
On the flip side, the growing demand for advanced, lightweight materials and the continued expansion of the commercial aviation market offer new opportunities for growth. Manufacturers that can embrace digital technologies, streamline their production processes and deliver high-performance products will be well-positioned to succeed in this evolving market.
Conclusion
The digital transformation of the aerospace manufacturing industry is reshaping the way aircraft and spacecraft are designed, produced and maintained. From large OEMs like Airbus and Boeing to specialised fastener manufacturers, companies across the aerospace sector are adopting digital tools to enhance efficiency and improve product quality.
As aerospace companies continue to push the boundaries of innovation, today’s manufacturers have a unique opportunity to contribute to the next generation of aerospace products. By embracing digital technologies and focusing on collaboration, these companies will play a critical role in shaping the future of aerospace manufacturing.
At JP Aero, we supply a wide range of fasteners. Whether standard, metric or custom design, we are leading UK experts.
Over the years we have built up a broad depth of knowledge around all types of fasteners in commercial aviation, heavy industry, oil & gas exploration, defence and now the space industry.
If you’re seeking to acquire innovative fasteners for the aerospace, aviation or any other industry, don’t hesitate to contact our dedicated team today. It would be our pleasure to provide you with any assistance you require.