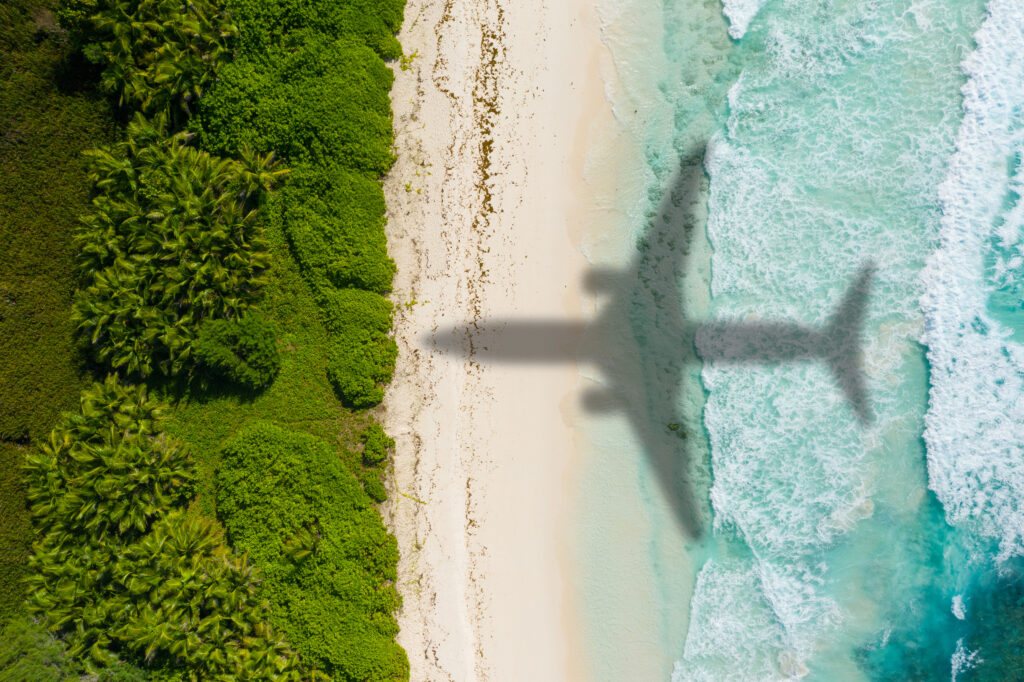
As electric aircraft begin to take centre stage, the aerospace industry is experiencing a transformative shift. The need for more sustainable (and quieter) air travel is growing, changing the fastener requirements needed for these cleaner vehicles. As such, these specialised fasteners become critical components that ensure the structural integrity and precision of cutting-edge aviation designs.
The Basics of Fasteners in Aircraft Construction
In aircraft construction, fasteners hold everything together – from the fuselage to the landing gear. But with electric aircraft, fastener requirements are more stringent due to the unique materials used and the need for lightweight (and strong) components. Screws, bolts, rivets and lockbolts play critical roles in aerospace, and with each comes a set of standards, like those set by the American National Standards Institute (ANSI), and other international bodies.
Electric aircrafts are pushing the boundaries of traditional fastener strength grades and material choices. The industry has to adopt new standards, including British fastener grades, to meet the needs of electric flight.
Electric Propulsion Systems: Unique Challenges for Fasteners
Electric propulsion systems are at the heart of electric aircraft, providing an eco-friendly alternative to traditional fuel-powered engines. These systems rely on electric motors, batteries, and high-efficiency power management technologies to drive the aircraft. However, electric propulsion places new demands on fasteners, particularly in terms of heat dissipation, vibration resistance, and weight management.
Fasteners used in electric propulsion systems must handle the constant mechanical stresses that come with high-frequency vibrations and the operational heat generated by electric motors. Tensile stress, torque type and dimensional specifications must be optimised to ensure that these fasteners can withstand the harsh conditions without compromising safety. Custom fasteners designed specifically for electric propulsion components are now more common – with a focus on lightweight materials that meet strict technical delivery conditions.
Fastener Materials: New Demands in Electric Aircraft
Fasteners used in electric aircraft must be lightweight, but they also need to meet high tensile grades. As such, traditional steel fasteners are being replaced by stainless steel fasteners, alloy and carbon steel to reduce weight without sacrificing strength. This shift in material choice improves the aircraft’s efficiency and maximises its battery life.
To meet the challenging requirements, materials like nickel base alloys and elastomer pressure springs are being integrated into electric aircraft fasteners. Lightweight tapping screws, rivets and spring lock washers increase durability amid the demands of modern aviation.
Compliance with Fastener Regulations and Standards
Electric aircraft development introduces new challenges regarding fastener regulations. The fasteners must comply with various international standards and maintain mechanical properties that are compatible with the lighter, more environmentally friendly materials used in construction. Standards such as ASTM A194 and ISO 4026, alongside DIN 6914 and DIN 7984, are just a few examples of regulations electric aircraft fasteners must meet.
To ensure compliance, dimensional specifications and technical delivery conditions must be carefully adhered to. The fasteners used in electric aircraft must withstand unique stresses and environmental conditions, leading to the development of compliant fasteners that meet the growing demand for durability and efficiency.
The Role of High-Strength Bolts in Electric Aircraft
One of the critical shifts in fastener design for electric aircraft is the reliance on high-strength bolts. Steel transmission tower bolts, commonly used in large-scale infrastructure, are being adapted for use in electric aircraft to offer high tensile strength while keeping the aircraft’s weight to a minimum.
Fastener torque is another critical consideration. In electric aircraft, the fasteners need to handle higher levels of torque due to the electric propulsion systems, which impose different mechanical stresses compared to traditional jet engines. This calls for fasteners with precise torque type specifications, such as those set by DIN 6924.
Custom Fastener Design for Electric Aircraft
Due to the uniqueness of electric aircraft, fastener design criteria is changing. Standard fasteners may not always be suitable, and custom fasteners are becoming the norm. These custom fasteners are often designed in-house to meet specific mechanical properties, such as resistance to extreme temperatures, vibration and fatigue.
Rivets and lockbolts secure batteries, electric motors and lightweight composite materials. Designing fasteners for these components requires adhering to strict specifications for parts. For example, shoulder screw grades and specifications for pins play a pivotal role in maintaining structural integrity and performance.
Looking Ahead: Innovations in Fastener Technology
As electric aircraft continue to evolve, fastener engineers must keep pace, create resistant bolts, make right fastener choices, and compare strength grades to enhance fastener performance and safety. New advancements in spring lock washers, medium type washers and hub attachment dimensions help electric aircraft to operate safely in various conditions.
The shift to electric aircraft is also driving innovation in fastener materials. Fasteners that comply with technical specifications and meet hardness limits are key to ensuring the long-term success of electric aviation. Additionally, tolerances on dimensions and standard equivalents are essential for developing fasteners that can be easily integrated into existing aircraft designs while supporting new technology.
Conclusion: Fasteners at the Forefront of Aviation Change
As electric aircraft become more mainstream, the fastener industry must adapt to meet new general fastener standards. From machine screws to rivets and steel hexagon nuts, fasteners play a crucial role in ensuring that electric aircraft can fly safely, efficiently and sustainably.
The future of electric aviation relies heavily on the development of fasteners that also meet stringent technical delivery conditions, adhere to specification of accessories and offer reliable performance. With ongoing advancements in fastener design criteria and the introduction of innovative materials, fasteners will continue to be the unsung heroes of the aerospace electric revolution.
At JP Aero, we supply a wide range of fasteners. Whether standard, metric or custom design, we are leading UK experts.
Over the years we have built up a broad depth of knowledge around all types of fasteners in commercial aviation, heavy industry, oil & gas exploration, defence and now the space industry.
If you’re seeking to acquire innovative fasteners for the aerospace, aviation or any other industry, don’t hesitate to contact our dedicated team today. It would be our pleasure to provide you with any assistance you require.