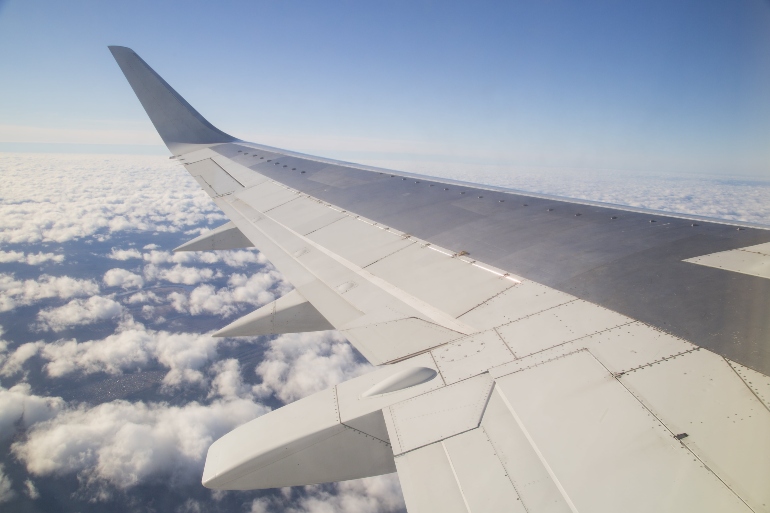
In the fast-paced world of aerospace engineering, innovation is paramount. As the demand for more efficient and sustainable aircraft continues to rise, engineers are turning to lightweight materials to meet these challenges. Lightweight materials have become a cornerstone in aerospace component design, offering a number of benefits that enhance structural performance, fuel efficiency, and overall sustainability. In this article, we will delve into the world of lightweight materials for aircraft applications, exploring their mechanical properties, applications in aerospace, and their role in shaping the future of aviation.
Seeking New Frontiers in Flight
From the pioneering days of aviation to the present, aerospace engineers have continuously sought new frontiers in flight, standing at the forefront of technological advancements and pushing the boundaries of what is possible. One of the key areas of focus has been the development of advanced materials that offer superior strength-to-weight ratios and enhanced durability. Composite materials, in particular, have revolutionised aerospace design, offering a lightweight alternative to traditional metal alloys.
What Are Composites?
Composite materials consist of two or more distinct materials combined to form a new material with unique properties. In aerospace applications, these materials typically include a combination of fibres, such as carbon or glass, embedded in a matrix, often made of epoxy resin. The resulting material is significantly lighter than conventional metals like aluminium or titanium, yet possesses comparable or even superior mechanical properties.
The use of composite materials in aerospace structures has become standard, thanks to their high strength-to-weight ratio, corrosion resistance, and fatigue performance. Aircraft manufacturers like Boeing have embraced composites in the design of next-generation aircrafts, such as the Boeing 787 Dreamliner. By incorporating composite materials into the aircraft’s fuselage, wings, and other components, Boeing was able to achieve significant weight savings, resulting in improved fuel efficiency and reduced operating costs.
Lightweight Metals for Next Generation Applications
In addition to composite materials, lightweight metals like aluminium alloys and titanium are crucial in aerospace design. These materials offer a unique combination of strength, durability, and weight savings, making them ideal for a wide range of aerospace applications. High-strength aluminium alloys, for example, are commonly used in the construction of aircrafts due to their excellent mechanical properties and ease of fabrication.
The world’s largest passenger aircraft, the Airbus A380, relies heavily on aluminium alloys for its structural components. While being lightweight, these alloys are exceptionally strong, allowing the A380 to accommodate the vast number of passengers it carries without compromising on performance or safety.
The aerospace industry is also exploring the use of advanced coatings and surface treatments to further enhance the performance of lightweight materials. Coatings can improve corrosion resistance, reduce friction, and enhance aerodynamic efficiency, ultimately contributing to the overall sustainability of aerospace structures.
Increased Sustainability: Bio-based Composites
Research into lightweight materials for aerospace applications is ongoing, with a focus on optimising microstructure and properties to meet the demanding requirements of modern aircrafts. Sustainable materials, such as bio-based composites and recycled metals, are also gaining traction as the industry strives to reduce its environmental impact.
For instance, aircraft manufacturers have begun incorporating bio-based composite materials derived from renewable sources such as plant fibres, soy, or flax into interior components like cabin panels, overhead bins, and seating. The adoption of bio-based composites in aerospace interior components represents a significant step towards achieving more sustainable and environmentally conscious air travel.
Lightweight Materials in Aerospace Fastener Manufacture
For all the reasons already discussed, composites and aluminium alloys are crucial in aerospace fastener manufacture and are utilised in the following ways:
Composite Fasteners: Composites, like carbon fibre reinforced polymers (CFRP), are increasingly used to manufacture fasteners in aerospace applications. These materials offer high strength-to-weight ratios, corrosion resistance, and excellent fatigue properties. Composite fasteners are commonly employed in non-structural components and interior fittings where weight reduction is critical. They contribute to overall fuel efficiency and help meet stringent weight restrictions in aerospace design.
Aluminum Alloy Fasteners: Aluminium alloys are widely used in fastener manufacture due to their lightweight nature and good mechanical properties. Aluminium fasteners offer high strength, corrosion resistance, and ease of fabrication. They are commonly used in both structural and non-structural applications throughout the aircraft, including fuselage panels, wing components, and interior fittings. Aluminium alloy fasteners contribute to weight reduction efforts without compromising on performance or safety.
Titanium Fasteners: While not as lightweight as composites or aluminium alloys, titanium fasteners are also used in aerospace applications for their exceptional strength-to-weight ratio and corrosion resistance. Titanium fasteners are commonly employed in critical areas of the aircraft where high strength and reliability are paramount, such as engine components, landing gear, and structural joints.
In conclusion, lightweight materials for aircraft applications are revolutionising design and shaping the future of aviation. From composite materials to lightweight metals and advanced coatings, these materials offer a host of benefits that improve structural performance, fuel efficiency, and sustainability. As the aerospace industry continues to evolve, the development of lightweight materials will remain a key area of focus, driving innovation and enabling the next generation of aircraft to take flight.
At JP Aero, we supply a wide range of fasteners. Whether standard, metric or custom design, we are leading UK experts.
Over the years we have built up a broad depth of knowledge around all types of fasteners in commercial aviation, heavy industry, oil & gas exploration, defence and now the space industry.
If you’re seeking to acquire innovative fasteners for the aerospace, aviation or any other industry, don’t hesitate to contact our dedicated team today. It would be our pleasure to provide you with any assistance you require.