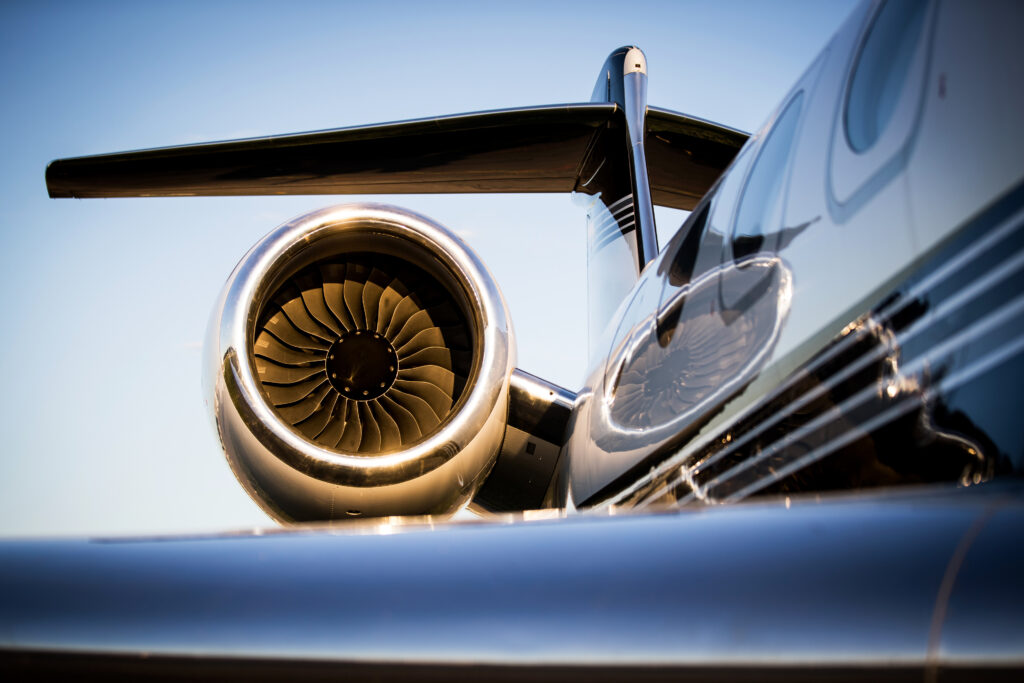
In modern aviation, designers constantly pursue weight reductions to improve fuel efficiency, enhance performance and lower operational costs. A significant contributor to this effort is the use of lightweight fasteners, small components that play a pivotal role in making aircraft lighter without compromising structural integrity or safety.
The Role of Lightweight Fasteners in Aircraft Design
Aircraft are complex systems composed of thousands of parts that must work together under extreme conditions. Traditional metal fasteners like steel bolts and nuts have been the standard for decades. However, the demand for lighter alternatives (due to fuel efficiency and performance goals) has spurred the development of advanced materials and methods that balance strength and weight reduction.
Lightweight fasteners, such as those made from titanium, aluminium and advanced polymers, provide exceptional durability while being significantly lighter than their traditional steel counterparts. These fasteners are increasingly being used in critical applications, including fuselage assembly, wings and sandwich panels used in cabin floors.
Key Benefits:
- Improved Fuel Efficiency
Reducing weight directly impacts fuel consumption. For every kilogram saved in an aircraft, airlines can achieve notable fuel savings over thousands of flight hours. Lightweight fasteners contribute to this by reducing the overall structural weight. - Enhanced Performance
A lighter aircraft is more agile, offers improved take-off and landing performance, and can carry higher payloads. These advantages translate into operational flexibility and greater efficiency for airlines. - Sustainability Goals
Weight reduction helps decrease carbon emissions, supporting the aerospace industry’s push toward greener operations. The adoption of lightweight products like advanced fasteners aligns with global sustainability objectives. - Adaptability to Modern Materials
Lightweight fasteners work seamlessly with modern materials like carbon composites, aluminium alloys and adhesives, which are increasingly used in aircraft manufacturing. This adaptability ensures structural integrity while maximising weight savings.
Challenges:
While the benefits of lightweight fasteners are clear, their adoption does come with challenges:
- Material Costs: Advanced materials like titanium and carbon composites can be more expensive than traditional metal fasteners.
- Corrosion Resistance: Lightweight materials may have reduced natural resistance to environmental factors compared to stainless steel, requiring additional protective systems or coatings.
- Strength vs. Weight Trade-offs: Achieving the right balance between strength and weight reduction demands precise engineering and testing.
- Integration with Existing Systems: Retrofitting lightweight fasteners into existing aircraft designs may require modifications to other parts and methods used in assembly.
Applications of Lightweight Fasteners in Aerospace
Lightweight fasteners are widely used in the assembly of:
- Fuselage Structures: Securely attaching sections while minimising overall weight.
- Wings and Control Surfaces: Ensuring structural integrity without adding unnecessary bulk.
- Cabin Interiors: Lightweight fasteners such as screws and bolts are ideal for attaching panels, seats and overhead compartments.
- Sandwich Panels: These multi-layered structures are a staple in modern aircraft design, and lightweight fasteners hold them together while preserving their low-weight advantage.
Future Trends in Lightweight Fastener Development
The aerospace industry is continually innovating, with new materials and technologies shaping the future of fastener engineering. Emerging trends include:
- Hybrid Fasteners: Combining lightweight materials with adhesives to improve strength and reduce weight further.
- Advanced Coatings: Developing coatings that enhance the durability and corrosion resistance of lightweight materials.
- Additive Manufacturing: The use of 3D printing to create custom fasteners tailored to specific applications.
Conclusion: The Importance of Lightweight Fasteners in Aviation
Lightweight fasteners are transforming aircraft design, offering substantial benefits in weight reduction, fuel efficiency and environmental sustainability. While challenges remain, continued innovation in materials and methods ensures that these critical components will play an even greater role in future aerospace advancements.
For aviation professionals seeking top-quality fasteners, at JP Aero, we provide a comprehensive range of lightweight fasteners to many industry sectors. Whether standard, metric or custom design, we are leading UK experts.
Over the years we have built up a broad depth of knowledge around all types of fasteners in commercial aviation, heavy industry, oil & gas exploration, defence and now the space industry.Contact us today to learn more about how our fasteners can support your weight reduction goals. It would be our pleasure to provide you with any assistance you require.