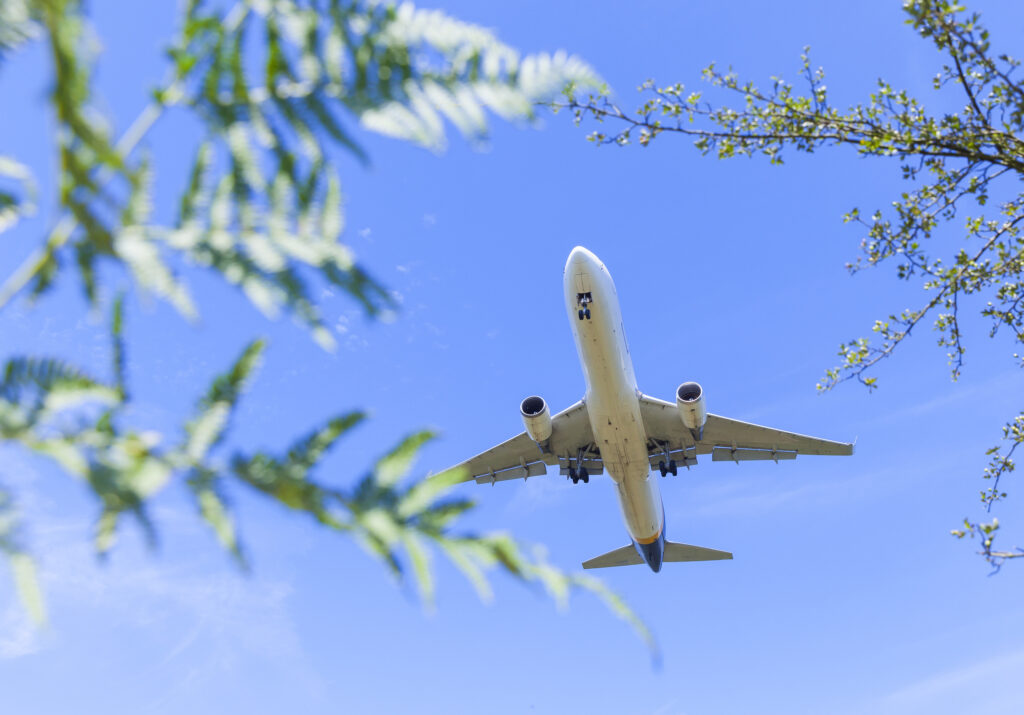
In the realm of aerospace engineering, sustainability has emerged as a critical focus area. As technology advances, so does the demand for environmentally responsible practices. One significant aspect of this shift is the manufacturing of aerospace fasteners. Here, we delve into the sustainable practices being adopted in the production of special fasteners, bolts, and other essential components, with a particular emphasis on the United Kingdom’s contribution to this evolving industry.
The Role of Fastener Manufacturers in Sustainability
Fastener manufacturers play a pivotal role in the aerospace industry, providing a wide array of products, including special fasteners, screws, bolts, and nuts. These components are integral to the structural integrity and safety of aircraft. Traditionally, the manufacturing process for these parts has been resource-intensive, often involving significant energy consumption and waste generation. However, the industry is now witnessing a paradigm shift towards more sustainable practices.
Sustainable Practices in the Production of Special Fasteners
Special fasteners, which are designed for specific applications and stringent performance requirements, are at the forefront of this transformation. These bespoke fasteners often require customised production processes, which historically have had a higher environmental footprint. To mitigate this, fastener manufacturers are adopting several green initiatives:
Material Selection: Utilising recycled and sustainable materials is a key strategy. For instance, steel fasteners can be manufactured from recycled steel, reducing the demand for virgin raw materials and minimising the carbon footprint.
Energy Efficiency: Advanced manufacturing technologies, such as hot forging, are being optimised for energy efficiency. Hot forging, a process used to shape metal parts, can be energy-intensive. By upgrading to more efficient equipment and implementing energy-saving practices, manufacturers significantly reduce their energy consumption.
Waste Management: Reducing waste during the production of different fastener products, including washers and nuts, is crucial. Manufacturers are investing in technologies that enable more precise cutting and shaping, which minimises material waste. Additionally, recycling scrap metal from the production process helps in conserving resources.
Innovations in the Manufacturing of Bolts
Bolts are an essential component in aerospace applications and require exceptional strength and durability. The sustainability of bolt manufacturing has seen significant improvements through various innovations:
Additive Manufacturing: Also known as 3D printing, this technology allows for the production of complex bolt designs with minimal material waste. This method not only conserves resources but also enables the creation of parts that are lighter yet stronger, contributing to overall fuel efficiency in aircraft.
Coatings and Treatments: Sustainable coatings and surface treatments are being developed to enhance the durability and corrosion resistance of bolts. These treatments extend the lifespan of bolts, reducing the frequency of needing replacements – and the associated environmental impact.
Lifecycle Analysis: Conducting a comprehensive lifecycle analysis helps manufacturers understand the environmental impact of their products from raw material extraction to end-of-life disposal. By identifying areas for improvement, manufacturers can implement more sustainable practices across the entire lifecycle of bolts.
The Impact of the United Kingdom’s Aerospace Sector
The United Kingdom has been a leader in promoting sustainability within the aerospace industry. British fastener manufacturers are at the forefront of adopting and implementing green practices. The UK government supports these efforts through policies and initiatives aimed at reducing the aerospace sector’s carbon footprint.
Regulatory Compliance: Adhering to stringent environmental regulations ensures that fastener manufacturers in the UK maintain high standards of sustainability. These regulations cover various aspects, from emission controls to waste management practices.
Research and Development: Investment in R&D is crucial for advancing sustainable manufacturing technologies. The UK’s aerospace industry benefits from a robust network of research institutions and collaborative projects that drive innovation in sustainable practices.
Supply Chain Integration: Sustainable practices are not limited to the manufacturing process alone. UK manufacturers are working towards integrating sustainability throughout their supply chains. This includes sourcing raw materials responsibly, optimising logistics to reduce carbon emissions, and collaborating with suppliers who prioritise environmental stewardship.
The Importance of Sustainable Industrial Fasteners
Industrial fasteners, including drilling screws and standard fasteners, are essential across various sectors, not just aerospace. The principles of sustainability applied in aerospace fastener manufacturing can be extended to other industries to drive a broader impact.
Cross-Industry Applications: Techniques such as hot forging and the use of recycled materials can be applied to the production of industrial fasteners used in construction, automotive, and other sectors. This cross-industry application of sustainable practices amplifies the positive environmental impact.
Education and Training: Promoting sustainability requires a skilled workforce knowledgeable in green manufacturing practices. Educational programs and training initiatives focused on sustainable production techniques are essential for preparing the next generation of engineers and manufacturers.
Sustainability in aerospace fastener manufacturing is not just a trend but a necessity for the future of the industry. From special fasteners and bolts to screws and nuts, every component plays a role in this green transformation. Fastener manufacturers, particularly in the United Kingdom, are pioneering sustainable practices that reduce environmental impact, enhance efficiency, and promote the responsible use of resources. As these practices continue to evolve, they will set new standards for sustainability, not only in aerospace but across various industrial sectors, ensuring a greener, more sustainable future for all.
At JP Aero, we specialise in providing a diverse selection of quality fasteners for various fastener manufacturing applications. Whether you need standard, metric, or custom-designed fasteners, we’re the leading experts in the UK.
With years of experience, we have extensive expertise in fastener manufacturing for commercial aviation, heavy industry, oil & gas exploration, defence, and the burgeoning space industry.
If you’re looking to procure innovative fasteners for aerospace, aviation, or any other industry requiring robust fastener solutions, don’t hesitate to reach out to our dedicated team today. We’re here to assist you with any fastener-related needs you may have.