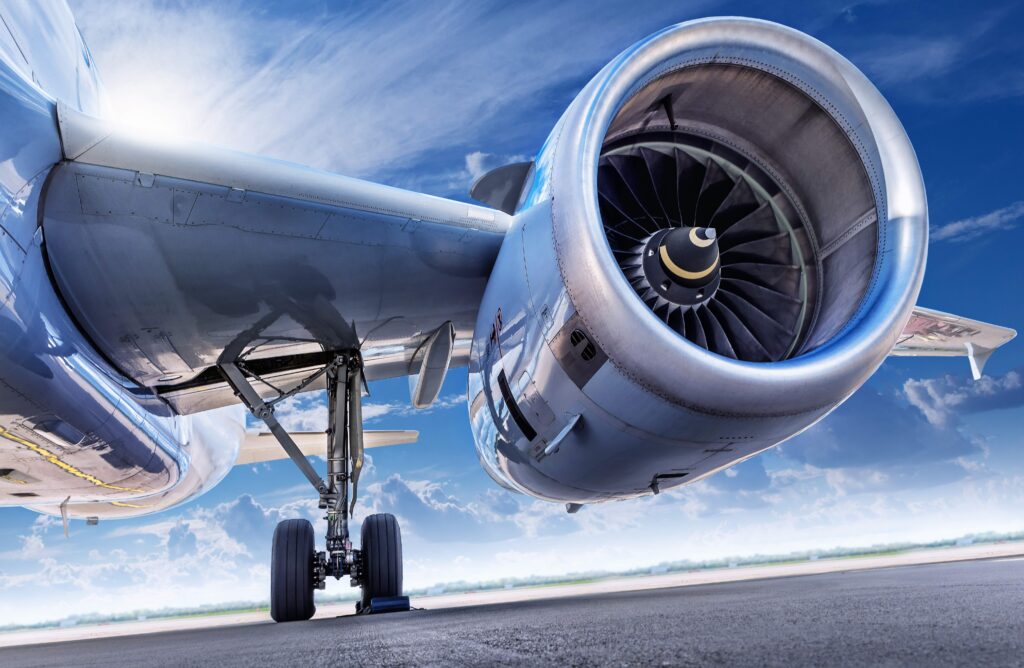
Comprehensive Guide to Torque Specification in the UK
In the realm of mechanical engineering and construction, torque specification plays a critical role in ensuring the integrity, safety, and reliability of various components and assemblies. From assembling intricate machinery to securing the nuts and bolts of a towering skyscraper, torque specifications provide a standardised approach to achieving the necessary tightness while preventing over-tightening that could lead to catastrophic failures.
In this comprehensive guide, we delve deeper into the importance of torque specifications, their application across industries, and best practices to ensure precision and safety.
Understanding Torque and Its Significance
Torque, in simple terms, is the rotational force applied to an object around an axis. In mechanical systems, it is crucial to apply the right amount of torque to achieve optimal performance and avoid potential issues. The torque specification is a predetermined value that dictates how much rotational force should be applied to fasteners like bolts, nuts, and screws during assembly.
The significance of torque specifications lies in achieving consistent tension across fasteners. Over-tightening can result in threads being stripped, fasteners breaking, or even structural damage due to excessive stress. On the other hand, insufficient torque can lead to loosening of fasteners over time, jeopardising the stability of the assembly. The torque specification acts as a safeguard against these potential pitfalls by providing a standardised guideline for the appropriate amount of rotational force to be applied.
Applications Across Industries
Torque specifications are pervasive across various industries, ranging from automotive and aerospace to construction and manufacturing. In the automotive sector, precise torque values are imperative for engine components, suspension systems, and safety-critical parts. Over-tightening a cylinder head bolt, for instance, could result in a cracked engine block, while under-tightening could lead to leaks and decreased performance.
In the aerospace industry, where safety is paramount, torque specifications are meticulously adhered to during the assembly of aircraft components. The tightness of fasteners on critical parts such as wings, landing gear, and engine mounts directly impacts flight safety and performance.
In construction, torque specifications find application in securing structural elements, fastening joints, and assembling heavy machinery. For instance, in the erection of steel structures like bridges and skyscrapers, following the correct torque specifications ensures the stability and longevity of the structure.
Best Practices for Torque Application
Use of a Torque Wrench: A torque wrench is an essential tool for applying torque accurately. It allows the user to set the desired torque value and alerts them when that value is reached, preventing over-tightening. There are various types of torque wrenches, including click-type, beam-type, and electronic torque wrenches, each suited for specific applications.
Clean and Lubricate Threads: Before applying torque, it’s important to ensure that the threads of fasteners are clean and free from debris or rust. Applying a suitable lubricant to the threads can help achieve more accurate torque values and prevent galling.
Uniform Application: Torque should be applied uniformly across multiple fasteners in an assembly to ensure consistent tension. This is particularly important when dealing with components that require even distribution of stress, such as gaskets.
Consider Material Properties: Different materials have varying levels of elasticity and strength. Torque values should be adjusted based on the material being used to prevent damage or deformation.
Follow Manufacturer Specifications: Manufacturers provide torque specifications for their products based on extensive testing and engineering analysis. Always refer to the manufacturer’s guidelines to ensure proper torque application.
Calibration and Maintenance: Regularly calibrate torque wrenches to maintain accuracy. Over time, these tools can lose precision, leading to incorrect torque values. Routine maintenance ensures consistent results.
Account for Friction: Friction between the fastener and the material can impact torque application. Be aware of the type of material and any surface treatments that might affect friction.
Safety Measures: When applying torque, wear appropriate personal protective equipment and ensure that the work area is safe and well-lit. This not only protects the assembler but also ensures accurate torque application.
Importance of Training and Skill
Beyond the tools and techniques, the knowledge and skill of the operator play a crucial role in torque application. Trained personnel understand the nuances of torque application, such as the tactile feedback a torque wrench provides when the specified value is reached. They can also account for variations that may arise due to environmental conditions, like temperature changes affecting material properties.
In industries where safety is paramount, such as nuclear power plants or medical equipment manufacturing, specialised training in torque application is often mandatory. These professionals are well-versed in the criticality of proper torque and the potential consequences of inadequate tightening.
Torque Specification Guide – Conclusion
In the intricate world of mechanical assemblies, adhering to proper torque specifications is more than just following guidelines; it’s about ensuring the reliability, safety, and longevity of the final product. From the automotive industry to construction sites and aerospace facilities, torque specifications provide the foundation for precision and quality.
By understanding the fundamentals of torque, its significance, and following best practices, engineers and technicians can navigate the complexities of torque application with confidence, leading to successful and secure mechanical assemblies. The synergy of precise tools, proper techniques, and skilled operators ensures that the rotational force applied to a bolt today transforms into the foundation of a safer and more reliable tomorrow.
Presenting JP Aero – Your Premier Aviation Fastener Supplier
At JP Aero, we take pride in being your ultimate source for an extensive array of aviation fasteners. Whether you require standard, metric, or intricately customised designs, our expertise stands as a testament to our leadership in the UK.
Throughout our journey, we have accumulated a comprehensive wealth of expertise spanning a diverse spectrum of fasteners. Our insights encompass the realms of commercial aviation, heavy industries, oil and gas exploration, defence applications, and now, even the burgeoning space sector.
Our commitment to serving your needs is unwavering. If you’re seeking to acquire top-tier aircraft fasteners, don’t hesitate to connect with our dedicated team today. It would be our pleasure to provide you with any assistance you require, helping you navigate the intricacies of aviation fasteners with utmost ease and confidence.