Aerospace Grade Fasteners: Enhancing Safety and Performance in the Aerospace Industry
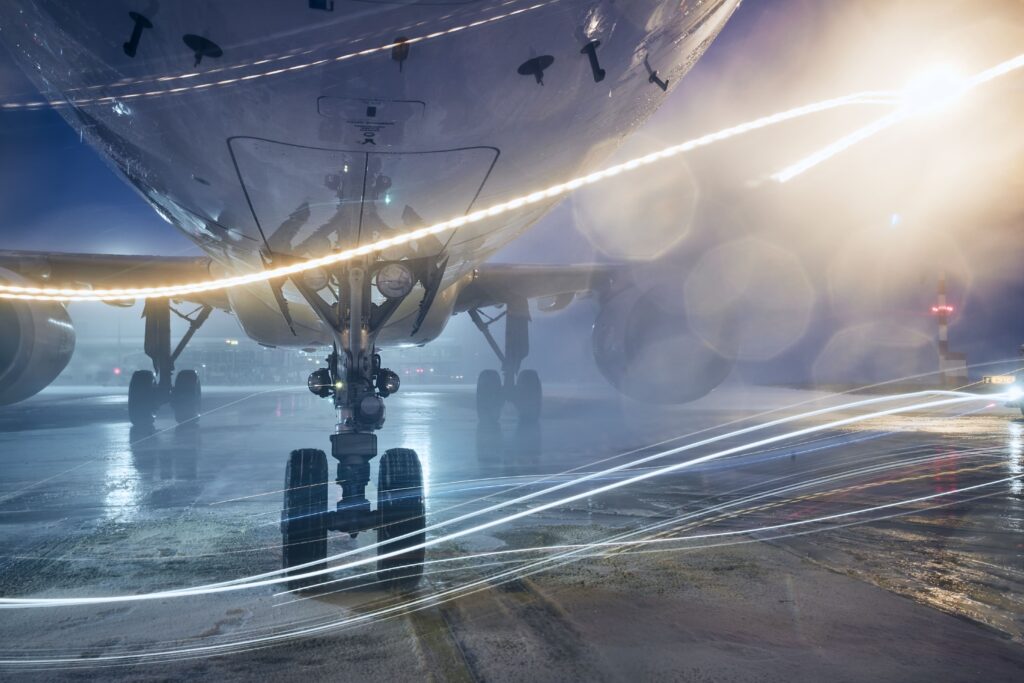
Aerospace grade fasteners play a crucial role in ensuring the safety, reliability and performance of aerospace applications.
These specialised fasteners, manufactured to stringent standards, provide secure connections to withstand the demanding conditions of the aviation and aerospace industries, such as the wide range of temperatures, from extremely cold conditions at high altitudes to the intense heat generated by atmospheric re-entry.
In the assembly of rocket engines, for example, whether used in space-bound rockets or satellite launch vehicles, fasteners securely connect various components of the engine, such as the combustion chamber, nozzle and turbopump, to ensure that the engine remains structurally sound and can withstand the high pressures, vibrations and temperatures encountered during rocket propulsion.
This article addresses the question ‘what are aerospace grade fasteners’ and explores their characteristics, applications and ability to withstand high pressures, temperatures and exposure to burning rocket fuel.
Understanding Aerospace Grade Fasteners
Aerospace grade fasteners differ from standard fasteners in terms of material, manufacturing standards and performance capabilities – ultimately designed to meet the unique requirements of the aviation and aerospace industries.
Many manufacturers opt for stainless steel in the fabrication of fasteners due to its excellent corrosion resistance, strength and durability. It’s also resistant to oxidation and scaling and can withstand high temperatures, maintaining its integrity even in environments exceeding 500°C.
Furthermore, stainless steel fasteners exhibit excellent mechanical properties, including high tensile and fatigue strength, which are essential for withstanding the demanding forces and vibrations experienced during flight and space missions.
Applications and Importance
Aerospace grade fasteners find extensive use in aircraft and space-bound rockets. They are employed in critical areas such as aircraft structures, engines, wings and control surfaces.
Looking at the assembly of aircraft wings, in particular, their structures require secure and reliable connections to ensure the structural integrity of the aircraft during flight. High-strength bolts and rivets hold various components together, including wing skins, ribs and spars. These fasteners stabilise and strengthen the wings to withstand the aerodynamic forces, vibrations and loads experienced during flight.
In the aerospace industry, where safety is paramount, the use of high-quality, high-tensile fasteners is vital to prevent failure.
Challenges and Performance Requirements
Aerospace fasteners face unique challenges due to the exposure to burning rocket fuel, high pressures and extreme temperatures. Fasteners used in space-bound rockets must withstand the intense forces and vibrations experienced during launch and when leaving the Earth’s atmosphere.
The engine compartment of an aircraft is subjected to extreme temperature variations, high humidity levels and exposure to corrosive agents such as engine fluids and saltwater during flights over coastal regions.
This is why stainless steel fasteners with high corrosion resistance are utilised to prevent rust and degradation caused by moisture and corrosive substances. These fasteners maintain their integrity even in the harsh conditions encountered in the engine compartment, ensuring the reliable and safe operation of the aircraft.
Manufacturing Standards and Materials
To meet stringent industry demands, aerospace grade fasteners are manufactured to precise standards, including specifications for materials, dimensions, mechanical properties and surface treatments.
Precise dimensions are crucial for preventing issues such as loosening or failure due to improper fit. Surface treatments are applied to aerospace fasteners to enhance their performance and durability, including coatings such as black oxide, zinc plating or other specialised finishes.
Surface treatments improve corrosion resistance, lubricity and wear resistance, extending the lifespan of the fasteners and reducing the risk of failure.
Types of Aerospace Fasteners
Aerospace grade fasteners encompass a wide range of products, including bolts, nuts, screws and rivets. Each type has a specific design and manufacturing consideration. For instance, aircraft bolts are often made of high-strength steel or titanium alloys to withstand high tensile, shear and fatigue loads.
Stainless steel fasteners can handle high loads without elongation or failure. Additionally, they exhibit excellent shear strength, which refers to their ability to resist forces acting parallel to the direction of the bolt. Shear loads commonly occur when components are subjected to lateral or sliding forces.
Titanium alloy bolts, on the other hand, offer a unique combination of high strength and low weight, i.e. an excellent strength-to-weight ratio, making it a preferred choice for aerospace applications.
By incorporating these design and manufacturing considerations, aerospace fasteners ensure secure and reliable connections in the aviation and aerospace industries.
Performance Characteristics
Aerospace fasteners must possess exceptional mechanical properties to ensure reliable performance. High strengths, both in tension and shear, are crucial to withstand the forces experienced in flight. Fasteners must also demonstrate fatigue resistance to withstand repeated loading cycles without failure.
Due to the extreme environments encountered in the Aerospace industry, safety considerations are paramount. As such, these fasteners play a crucial role in ensuring the safety and reliability of aircraft and space-bound rockets.
These fasteners provide secure connections, even in the face of high pressures, extreme temperatures and exposure to burning rocket fuel. As the aerospace industry continues to advance, the development of innovative fasteners remains crucial to meet evolving performance requirements.
About JP Aero
We supply a wide range of aviation fasteners. Whether standard, metric or custom design, we are leading UK experts.
Over the years we have built up a broad depth of knowledge around all types of fasteners in commercial aviation, heavy industry, oil & gas exploration, defence and now the space industry.
To find out more about procuring aircraft fasteners, contact our team today, and we will be happy to help in any way we can.